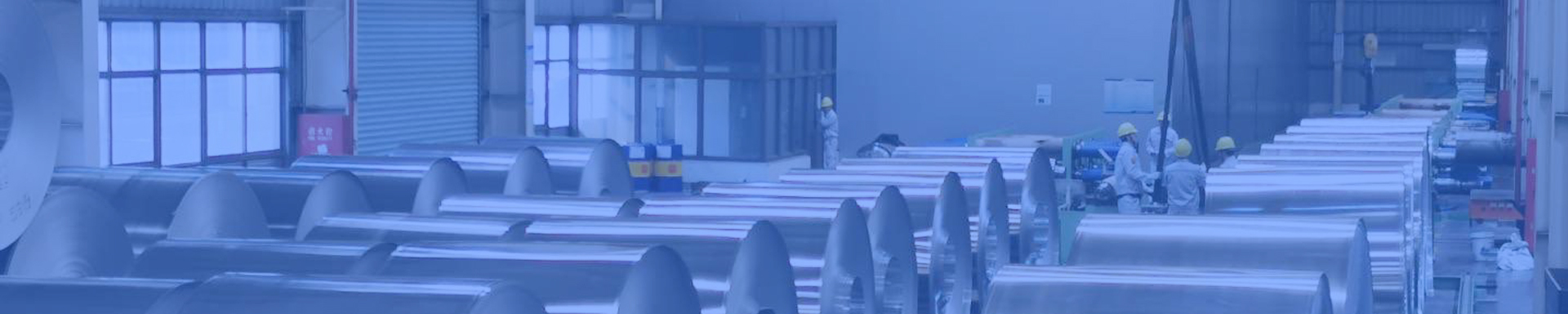
Hot Rolling Mill Machine Of The Operate Side Work Roller Rolling Mill Block Shaft
Our advantages: High-precision intelligent CNC manufacturing equipment, high-tech staff, mature processing system, strict quality inspection process, high-precision inspection instruments, excellent production management process, is the guarantee of high-quality products.
Our company has DMG DMF1800*600 five-axis machining center, horizontal machining center,vertical machining center,gantry machining center and high-precision three-coordinate inspection.Machine 80% of the equipment is CNC machine tools;Powerful equipment, so that we get strong quality assurance in product manufacturing and processing.
- Guangwei Manufacturing Precision
- Henan,Luoyang
- Contractual Stipulation
- Information
Hot Rolling Mill Machine Of The Operate Side Work Roller Rolling Mill Block Shaft
Application scenarios of the working roll frame shaft on the operating side of the hot rolling mill
Function: Support the work roll, withstand high loads, impact forces, and friction during the rolling process, and adapt to high temperature, high humidity, and dusty environments.
Typical operating conditions:
High temperature (roll surface temperature can reach over 600 ℃ during rolling);
High cyclic stress (frequent start stop and variable load);
It needs to resist oxidation and wear.
Material selection of the working roll frame shaft on the operating side of the hot rolling mill
Common materials:
Alloy structural steel, such as 42CrMo and 40CrNiMoA, has high strength, toughness, and wear resistance.
Tool steel: such as H13 (4Cr5MoSiV1), suitable for higher temperature and wear resistance requirements.
Stainless steel: such as 17-4PH (precipitation hardening type), used in corrosive environments.
Selection criteria:
Tensile strength (≥ 800 MPa), fatigue limit, high temperature stability;
Balance between cost and processing performance.
Heat treatment process of the working roll frame shaft on the operating side of the hot rolling mill
Key steps:
Quenching and tempering treatment (quenching+high temperature tempering):
Quenching: Oil quenching at 850~880 ℃ to obtain martensitic structure;
Tempering: 550~650 ℃, to eliminate stress and improve toughness.
Surface strengthening (optional):
Induction hardening: local hardening of the shaft neck, depth 2-5mm, hardness HRC50-55;
Nitriding treatment: Gas nitriding or ion nitriding, surface hardness ≥ HV900, improves wear resistance.
Stress relief annealing: Eliminating residual stress before precision machining.
The production of the work roll frame shaft of the hot rolling mill emphasizes the high strength of the material, the precision of the heat treatment process, and the strict inspection of the manufacturing process. By reasonable material selection and process control, the lifespan of components can be significantly extended (usually designed for 5-10 years), and the maintenance cost of rolling mills can be reduced. In actual production, parameters need to be adjusted according to the specific rolling mill model (such as 2050mm hot rolling mill) and rolling materials (such as stainless steel and carbon steel).
Main Products:All kinds of mill (roll) bearing block, bending roll block and other mill precision parts, the accuracy of these products directly affects the accuracy of the mill directly affects the quality of products produced by the mill.
The type is the operate side of work roller rolling mill block shaft of mill work roll intermediate roll support roll, and can also accept other non-standard customizing from customers.
The Operate Side Of Work Roller Rolling Mill Block Shaft Product Process
The company has formed a set of mature mechanical processing technology for the production of bearing housing through the accumulation of long-term experience: