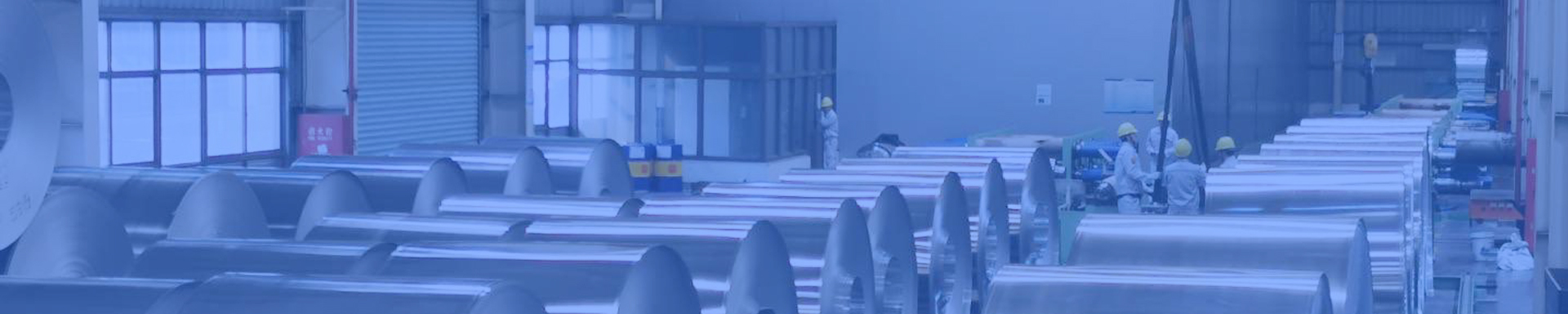
Hot rolling mill drive side work roll shaft body
Application scenarios of the working roll shaft body on the drive side of the hot rolling mill
Core functions
Power transmission: The torque of the main motor or gearbox is transmitted to the working roll shaft, driving the roll to rotate and complete the rolling process.
Load bearing capacity: capable of withstanding rolling forces (up to thousands of tons), alternating torque, and impact loads (such as biting and throwing moments).
Precision control: By designing with high rigidity, the radial runout of the rolling mill is ensured to be ≤ 0.05mm, ensuring the accuracy of the strip thickness.
- GW Precision
- China,Luoyang
- Contractual Stipulation
- Anual Capacity is 1000 pieces
- Information
The Drive Side Work Roller Shaft Body
Performance characteristics of the working roll shaft on the drive side of the hot rolling mill
Materials and Heat Treatment
Material selection:
34CrNiMo6 (German standard): High strength, high toughness, excellent fatigue resistance (mainstream choice).
42CrMo4 (medium load condition): Low cost, strength meets the standard after quenching and tempering (σ ₆ ≥ 900MPa).
GW precision has formed a set of mature mechanical processing technology for the production of working roll shaft through the accumulation of long-term experience:
Heat treatment process:
Quenching and tempering treatment (quenching 850 ° C+tempering 550-600 ° C), hardness HRC 28-32.
Induction hardening of the journal surface (HRC 50-55) enhances wear resistance.
Key performance parameters of GW working roll shaft
Typical values of indicators/required testing conditions
Dynamic torque simulation test with torque capacity of 100-800 kN · m
Fatigue limit ≥ 350 MPa (10 ⁷ cycles) ISO 1143
Axial stiffness ≤ 0.08 mm deformation (full load) laser displacement detection
Short term temperature resistance of 600 ° C, long-term ≤ 250 ° C thermocouple monitoring
Special design features
Universal joint connection: using a cross axis universal joint to compensate for roll deflection (angle ≤ 3 °).
Cooling structure: Hollow shaft with circulating water or external spray to control thermal deformation (Δ T ≤ 50 ° C).
Overload protection: The hydraulic safety coupling automatically disengages when the torque exceeds the limit.
Analysis of the advantages of the working roll shaft body on the drive side of the hot rolling mill
High load-bearing efficiency
Alloy steel material+optimized section design, torque transmission efficiency ≥ 97%.
Fast dynamic response
Hollow shaft reduces weight by 20-30% and is suitable for high-speed rolling (rolling speed ≥ 15 m/s).
Long-Life Technology
Surface quenching+nitriding treatment, with a wear resistance life of 5-8 years (annual rolling volume of millions of tons).
The selection and manufacturing of hot rolling mills require comprehensive consideration of the type of rolling mill, rolling materials, and operating conditions. High chromium cast iron and high-speed steel rollers are suitable for high wear resistance scenarios, while forged steel rollers are more suitable for high load rough rolling. Strict control of heat treatment and machining accuracy is required in manufacturing to ensure thermal fatigue resistance and wear resistance.
GW precision has varieties of VMC and HMC for production.Powerful equipment, so that we get strong quality assurance in product manufacturing and processing.
Perfect quality management system, effective after-sales service guarantee, so that the company's working roll shaft products won a good reputation.
Time is money,make the call now!