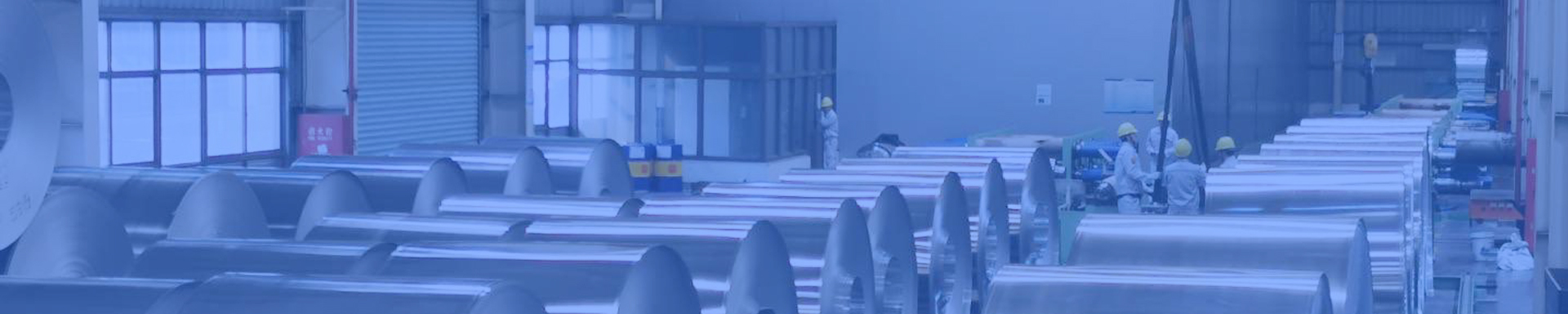
Hot Rolling Mill Machine Of Operate Side Work Roller Rolling Mill Block Shaft
Our company has DMG DMF1800*600 five-axis machining center, horizontal machining center,vertical machining center,gantry machining center and high-precision three-coordinate inspection.
- GW Precision
- China,Luoyang
- Contractual Stipulation
- Anual Capacity of Steel Spool is 4000 pieces
- Information
Hot Rolling Mill Machine Of Operate Side Work Roller Rolling Mill Block Shaft
Operating side work roll mill frame shaft of hot rolling mill
(Suitable for hot rolling production lines of plate and strip/section steel)
1、 Application scenarios
1. Core functions
Roller positioning and force transmission:
Maintain the stability of the working roll under the action of rolling force (maximum 30MN) and bending force (± 1000kN)
Endure the instantaneous impact load of biting steel (impact coefficient 2.0-3.5)
Thermal management:
Working in a rolling temperature environment of 400-800 ℃, the instantaneous surface temperature can reach 300-450 ℃
Need to resist periodic thermal stress (>10 ⁵ cycles/year)
2. Typical working conditions
Mechanical load: Hertz contact stress 1000-1500MPa, torsional vibration load (critical speed should avoid working speed 1.5-2.5 times)
Wear environment: Iron oxide scale abrasive particles (HV800-1100)+rolling lubricant high-temperature carbonization deposition
Material selection and optimization of the working roll mill frame shaft on the operating side of the hot rolling mill
1. Base material
Material grade, core advantages, applicable scenarios
50CrMoV high temperature strength (σ 0.2 ≥ 650MPa at 500 ℃) wide and thick plate rolling mill (roll body>3m)
Low cycle fatigue performance (Nf ≥ 5000 times at Δ ε t=1%) of 38CrNiMoV high-strength strip steel during rolling
H13 improved heat-resistant cracking (thermal conductivity 24W/m · K) stainless steel hot-rolled
2. Key reinforcement technologies
Bearing mating surface:
Laser quenching (hardening layer depth 2-3mm, HRC54-58)
Plasma spraying WC-10Co4Cr (porosity<0.8%)
Threaded connection area: boronizing treatment (Fe2B layer 50-80 μ m)
3. Innovative material applications
Gradient functional axis:
Core: 25Cr2MoV (high toughness)
Surface: Stellite 21 (resistant to high temperature wear)
Diffusion bonding through hot isostatic pressing (HIP)
3. Heat treatment system
Vacuum quenching: 1020 ℃ × 3h (nitrogen cooling)
Double tempering: 560 ℃× 4h+520 ℃× 6h (oil cooled)
Stabilization treatment: Deep cooling (-120 ℃× 8h)+aging (250 ℃× 24h)
4. Surface strengthening
Composite processing:
Shot peening (Almen strength 0.4-0.45mmN)
Ionic sulfurization (FeS layer 1-2 μ m)
Laser texturing (Sa=3-5 μ m)
*Key processes:
Constant temperature grinding of bearing position (coolant 20 ± 1 ℃)
Electrochemical machining of transition fillet (R angle accuracy ± 0.05mm)*
Typical parameters of the working roll mill frame shaft on the operating side of the hot rolling mill
Requirements for parameter indicators
Axis diameter tolerance of φ 320 ± 0.008mm
High temperature creep rate ≤ 1 × 10 ⁻⁷%/h (500 ℃/200MPa)
Vibration acceleration ≤ 4.5m/s ² (ISO 10816-8)
The service life of this shaft in a hot rolling mill is 2-3 years (with an annual rolling capacity of 1.5-2 million tons), and it can be extended to 5 years using gradient materials. The proportion of thermal fatigue failure is greater than 60%, and the current research and development focus is on nanostructured thermal barrier coatings.