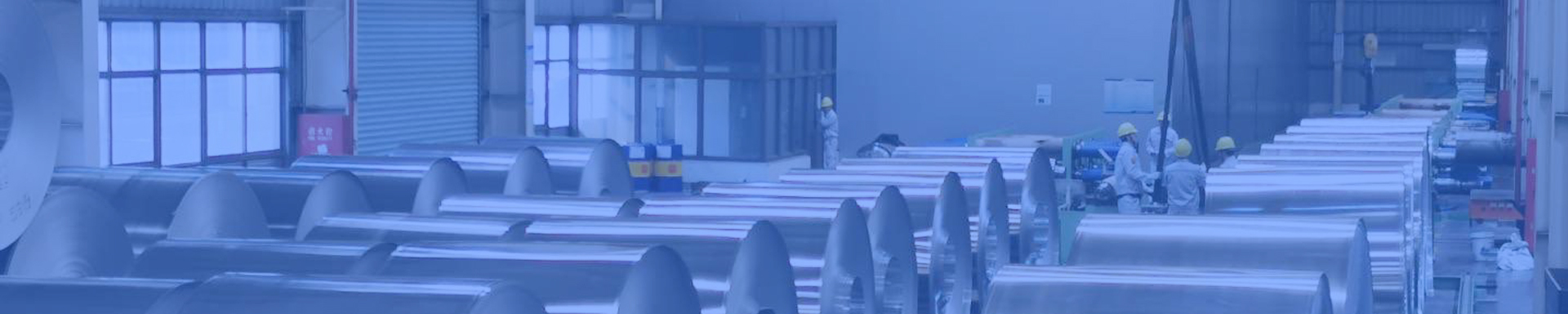
Hot Rolling Mill Machine Of The Operate Side Work Roller Block Shaft
GW precision have upgrade the workshop with more than 90% equipment to be CNC maching center for our work roller block.
- GW Precision
- China,Luoyang
- Contractual Stipulation
- Information
Hot Rolling Mill Machine Of The Operate Side Work Roller Block Shaft
Application scenarios of the bearing seat of the working roll group on the operating side of the hot rolling mill
The bearing seat of the operation side work roll group is the core component of the hot rolling mill, responsible for supporting the work rolls, transmitting rolling force, and ensuring precise positioning of the rolls. Its typical applications include:
High temperature and high load environment
Production lines for hot-rolled strip steel, thick plates, profiles, etc. (rolling temperature 800~1200 ℃).
It can withstand rolling forces up to 10000~30000 kN and needs to resist thermal deformation and fatigue.
High speed rolling mill (such as hot rolling mill)
The rolling speed can reach 15-30 m/s, and the bearing seat needs to have high dynamic stability.
Frequent roller changing conditions
Hot rolling rolls need to be replaced every 4-8 hours, and bearing seats need to be designed for quick disassembly and assembly.
Material selection for the bearing seat of the working roll group on the operating side of the hot rolling mill
1. Material of bearing seat body
High strength cast iron:
HT300: Low cost, suitable for small and medium-sized rolling mills.
QT600-3 ductile iron: better heat resistance and fatigue resistance.
Cast/forged steel:
ZG35CrMo/ZG42CrMo: The preferred heavy-duty rolling mill is resistant to high temperature deformation.
34CrNiMo6 forged steel: ultra-high strength, used for high-end rolling mills.
2. Wear resistant/heat-resistant components
Bearing liner plate:
Copper alloy (ZCuSn10Pb10): resistant to high temperature wear (≤ 300 ℃).
Composite material (PTFE+copper powder): self-lubricating, reduces maintenance.
Cooling water channel material:
Stainless steel (316L): prevents corrosion from cooling water.
The manufacturing of the operating side bearing seat of the hot rolling mill needs to take into account high temperature strength, wear resistance, and heat dissipation efficiency. The core process includes:
High density casting/forging ensures substrate strength;
Precision machining and heat treatment ensure dimensional stability;
Optimizing the cooling system extends its service life.
Through modular design and intelligent monitoring (such as embedding temperature sensors), the reliability and efficiency of the hot rolling production line can be further improved.
Bearing Blocks are one of GW precision main products in the non-ferrous metal industry.GW precision also accept non-standard customizing from customers.
The bearing block accuracy affects the non-ferrous metal product quality produced by the mill.
If there is any inquiry for work roller and support roller block or any technology questions, welcome to contact with us for assist.
guangwei@gwspool.com