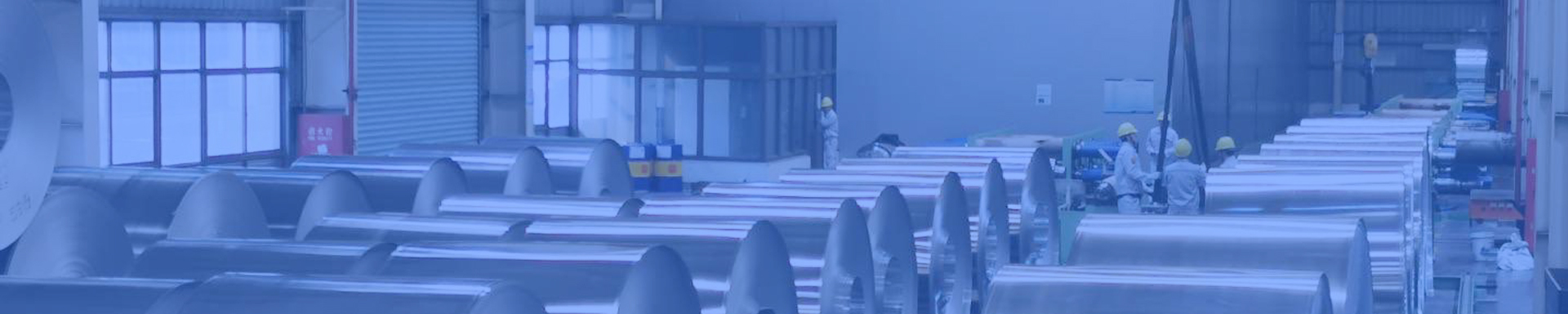
The Casting Steel Bearing Block
In the various components of the mill ,GW Precision bearing seat is an important component of the mill, it has high precision requirements.
Material:
working roll (forgings):45 steel,40Cr,42CrMo
support roll (castings): zg310-570, zg270-500.
- GW Precision
- China,Luoyang
- Contractual Stipulation
- Information
Supporting Roller Of The Casting Steel Bearing Block
Typical application scenarios and technical indicators of cast steel bearing seats
1. Hot rolling production line (high temperature and heavy load)
Operating condition parameters
Rolling force: 2000-8000 tons
Working temperature: 200-600 ℃ (local peak 800 ℃)
Cooling water pressure: 10-15MPa
Typical lifespan: 3-5 years (rolling capacity of 3-6 million tons)
Representative model
2250mm hot rolling mill (supporting roller bearing seat)
5500mm wide and thick plate rolling mill (work roll bearing seat)
2. Cold rolling production line (high-precision)
Operating condition parameters
Rolling force: 500-3000 tons
Rolling speed: 10-30m/s
Dimensional accuracy requirement: bearing hole roundness ≤ 0.01mm
Typical lifespan: 5-8 years (rolling capacity of 2-4 million tons)
Representative model
Six roll UCM cold rolling mill (middle roll bearing seat)
Twenty roll Sendzimir rolling mill (backing bearing seat)
3. Special rolling mill (extreme environment)
Copper/Aluminum Rolling Mill
Corrosion resistance requirement: pH 3-11 range
Lightweight design: reduces weight by 15-20% compared to steel mills
Stainless steel rolling mill
Anti adhesive steel design: Contact surface hardness ≥ HRC55
Material technical parameters of cast steel bearing seat
1. Performance comparison of mainstream materials
Material grade Yield strength (MPa) Impact energy (J) Maximum working temperature (℃) Applicable rolling mill type Cost coefficient
ZG270-500 270 25 350 Light Cold Rolling Mill 1.0
ZG35CrMo 550 40 450 Medium sized Hot Rolling Mill 1.8
ZG42CrMo 650 35 500 heavy-duty hot rolling mill 2.2
ZG06Cr13Ni4Mo 750 60 550 Stainless Steel/Special Rolling Mill 3.5
2. The role of alloying elements
Cr(1.0-1.5%): Improve hardenability and oxidation resistance
Mo(0.2-0.6%): Inhibit high-temperature tempering brittleness
V(0.1-0.3%): Grain refinement (ASTM grade 8 or above)
Ni(4-6%): Improve low-temperature toughness (-40 ℃ impact energy ≥ 40J)
3、 Manufacturing key parameters
1. Casting process parameters
Control standards for key process parameters
Melting medium frequency furnace temperature 1600 ± 20 ℃, oxygen content ≤ 20ppm
Bottom pouring speed of 1.5-2.5kg/s, riser volume ratio of 15-20%
Heat treatment normalizing at 900 ℃ for 4 hours+tempering at 600 ℃ for 6 hours residual stress ≤ 80MPa
2. Mechanical processing parameters
Processing type equipment/tool accuracy requirements
Bearing hole precision machining CNC boring machine (diamond tool) IT6 level, cylindricity ≤ 0.01mm
Sealing groove machining vertical machining center (CBN blade) symmetry ≤ 0.02mm
Screw hole CNC drilling center (extrusion tap) with 6H level accuracy
3. Surface treatment parameters
Performance improvement effect of processing technology parameters
Ion nitriding at 520 ℃ for 30 hours, ammonia decomposition rate of 30-40%, surface hardness HV900-1000
Laser cladding of Ni60+30% WC with a layer thickness of 0.8mm increases wear resistance by 5 times
Micro shot peening steel shot with a diameter of 0.2mm and a strength of 0.3mA extends fatigue life by 2 times
GW Precision has formed a set of mature mechanical processing technology for the production of bearing housing through the accumulation of long-term experience.
With perfect quality management system and effective after-sales service guarantee, GW Precision products won a good reputation.