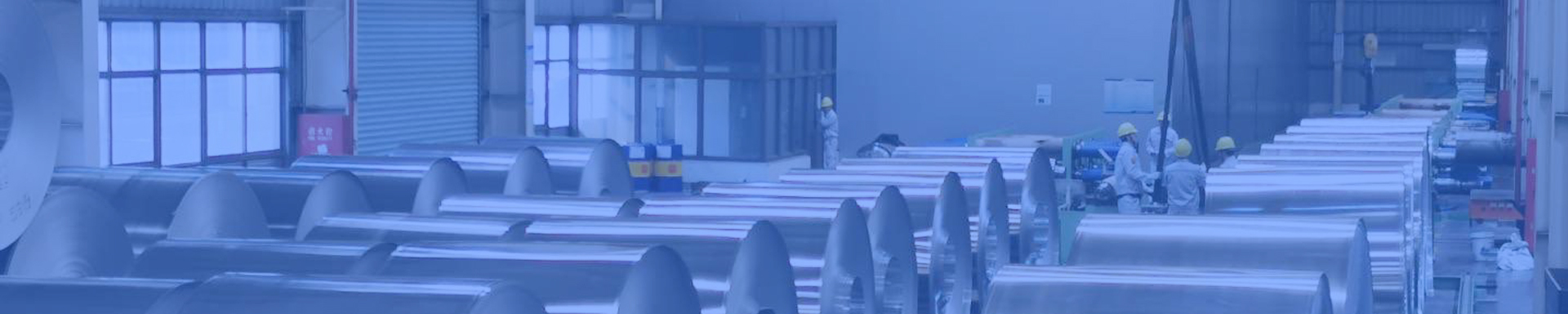
Rolling Mill Bearing Block Of Supporting Roller Of Hot Mill Machine
Material:
working roll (forgings):45 steel
support roll (castings): zg310-570,
Our advantages: High-precision intelligent CNC manufacturing equipment, high-tech staff, mature processing system, strict quality inspection process, high-precision inspection instruments, excellent production management process, is the guarantee of high-quality products.
- Guangwei Manufacturing Precision
- Henan,Luoyang
- Contractual Stipulation
- Anual Capacity of Steel Spool is 4000 pieces
- Information
Rolling Mill Bearing Block Of Supporting Roller Of Hot Mill Machine
The use function of the bearing seat of the supporting roll rolling mill of the hot rolling mill
Core functions
Support and positioning: bear the huge radial force (up to thousands of tons) during the rolling process, ensuring stable rotation of the support rollers.
Force transmission: The rolling force is transmitted to the frame through bearings to maintain the accuracy of the roll gap (± 0.1mm level).
Sealing and lubrication: The built-in sealing system prevents the intrusion of cooling water and oxide scale, ensuring bearing lubrication (such as lithium grease or circulating oil).
Additional requirements
Impact resistance: able to withstand instantaneous impacts during rolling (such as dynamic loads during steel biting).
Thermal stability: Maintain dimensional stability under working conditions of 80-150 ℃ (considering thermal expansion coefficient matching).
Material selection for the bearing seat of the support roll rolling mill of the hot rolling mill
Mainstream materials
Cast steel:
ZG270-500 (medium carbon cast steel): Low cost, used for small and medium-sized rolling mills.
ZG35CrMo: Add Cr and Mo to enhance strength (tensile strength ≥ 650MPa) and fatigue resistance.
Forged steel:
42CrMo (hardness HB240-280 after quenching and tempering treatment): Used for heavy-duty rolling mills, it has better impact resistance.
Special treatment
Surface quenching: High frequency quenching of bearing mating surfaces (hardness HRC50-55) increases wear resistance by more than three times.
Low temperature annealing: eliminating casting stress (heating to 550 ℃ for insulation and then slow cooling).
Production and manufacturing technology process of bearing seat for hot rolling mill supporting roll and rolling mill
1. Casting process (taking ZG35CrMo as an example)
Mold design: Using 3D printed sand or wood molds, with a 5 ‰ shrinkage allowance reserved.
Melting: Medium frequency furnace melting (1550 ℃), online composition detection by spectrometer (C control 0.32-0.38%).
Pouring: Bottom pouring ladle to avoid slag inclusion, with a riser design of 1.5 times the size of the hot section to compensate for shrinkage.
Heat treatment:
Normalize (900 ℃× 4h)+temper (600 ℃× 6h), with grain size reaching ASTM grade 5 or above.
Mechanical processing of bearing seat for hot rolling mill support roll
Rough machining:
Longmen milling machine machining reference surface (flatness 0.1mm/m).
Lubrication channel for deep hole drilling (hole diameter Φ 20 ± 0.5mm).
Precision machining:
CNC machining of bearing holes (IT6 level precision, Ra1.6μm)。
Boring machine for machining bolt holes (with a positional tolerance of Φ 0.05mm).
The type is the bearing seat of mill work roll intermediate roll support roll, and can also accept other non-standard customizing from customers.