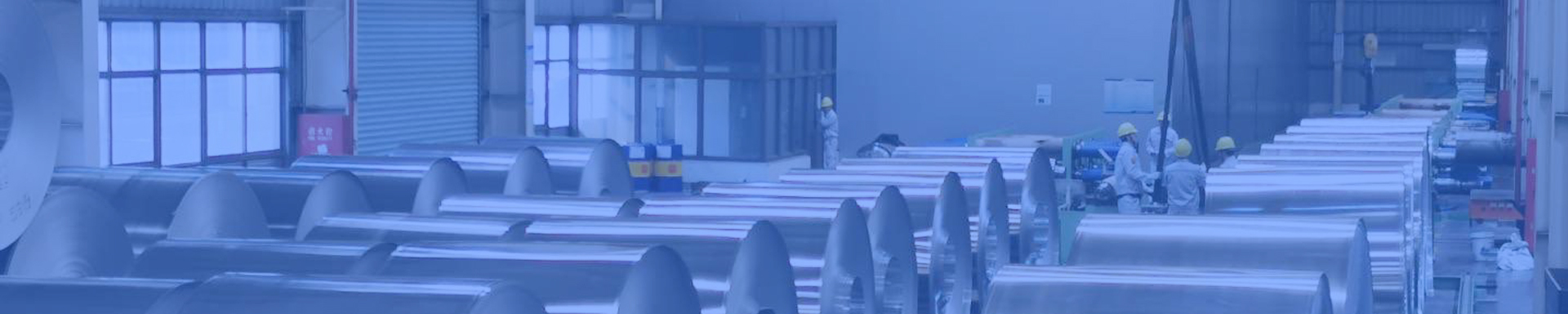
Rolling Mill Bearing Block Of Supporting Roller Of Cold Mill Machine
Application scenarios of bearing seats for cold rolling mill support rolls
1. Core functions
Support positioning: Accurately fix the support rollers, withstand rolling forces of up to thousands of tons and disperse them to the frame.
Force transmission: The rolling pressure is transmitted to the hydraulic pressing system through bearings to achieve roll gap adjustment.
Dynamic stability: Suppress rolling vibrations (such as harmonics caused by strip deviation or thickness fluctuations).
2. Typical application models
Multi roll cold rolling mill: such as Sendzimir 20 roll mill, four roll/six roll cold rolling mill (used for high-precision strip steel such as stainless steel and silicon steel).
Precision rolling line: an ultra-thin strip rolling mill with a thickness control accuracy requirement of ≤ 1 μ m.
- GW Precision
- China,Luoyang
- Contractual Stipulation
- Anual Capacity is 1000 pieces
- Information
Rolling Mill Bearing Block Of Supporting Roller Of Cold Mill Machine
Performance characteristics of Rolling Mill Bearing Block
1. Material and structural design
texture of material:
Cast steel (ZG35CrMoV): Strong fatigue resistance and moderate cost (mainstream choice).
Forged steel (42CrMo4): used for ultra heavy rolling mills, with a 20% increase in load-bearing capacity.
Structure:
Split box: The upper and lower halves of the box are pre tightened with hydraulic bolts (pre tightening force ≥ 1.5 times the working load).
Built in sensor slot: can integrate pressure sensors (measuring bearing load) and temperature probes.
2. Key performance parameters
Typical values of indicators/required testing conditions
Static bearing capacity 2000-5000 kN (single-sided) maximum rolling force condition
Dynamic stiffness ≥ 500 kN/μ m (axial) exciter frequency response test
Bearing temperature rise control ≤ 45 ° C (oil film bearing working condition) infrared thermal imaging monitoring
Sealing cleanliness NAS 1638 Class 6 (lubricating oil) particle counter detection
3. Special design features
Hydraulic labyrinth seal: an air seal with a pressure of 0.05-0.1MPa and multiple rubber lip seals to prevent emulsion from entering.
Quick roller changing system: The bottom of the bearing seat is integrated with a hydraulic lifting guide rail, and the roller changing time is ≤ 30 minutes.
Micron level alignment: using a wedge adjustment mechanism, the horizontal/vertical alignment accuracy is ≤ 0.01mm.
Key parameters for the production and manufacturing of hot rolling rolls
Chemical composition (taking high chromium cast iron as an example):
C: 2.5~3.5%, Cr: 12~20%, Mo: 1~3%, Ni: 0.5~1.5%, V: 0.5~1.5%。
Heat treatment process:
Quenching: Oil quenching or air cooling at 950~1050 ℃ to increase hardness.
Tempering: 400~550 ℃ to relieve stress and balance toughness and hardness.
Cryogenic treatment (optional): -70~-196 ℃ to enhance residual austenite transformation.
Mechanical properties:
Hardness: The surface hardness of the finishing roll is ≥ 70 HS (Shore hardness), and the surface hardness of the roughing roll is ≥ 55 HS.
Tensile strength: ≥ 800 MPa (forged steel rollers can reach over 1200 MPa).
Impact toughness: ≥ 15 J/cm ² (core requirement).
Manufacturing process:
Casting: Centrifugal casting is used for composite rollers (outer wear-resistant material+core tough material).
Forging: Steel rollers require multi-directional forging to refine grain size.
Processing accuracy: roller diameter tolerance ± 0.05mm, roughness Ra ≤ 0.8 μ m.
Cooling and lubrication:
Internal water cooling of the rolling mill (water temperature 20-40 ℃, flow rate ≥ 5m/s).
Rolling lubrication uses graphite or synthetic lubricants to reduce steel sticking.
In the production process of rolling mill bearing block bending roll block and other products, the optimized processing program is compiled by computer, and the process plan is arranged reasonably, which ensures the product quality to reach the international first-class standard.