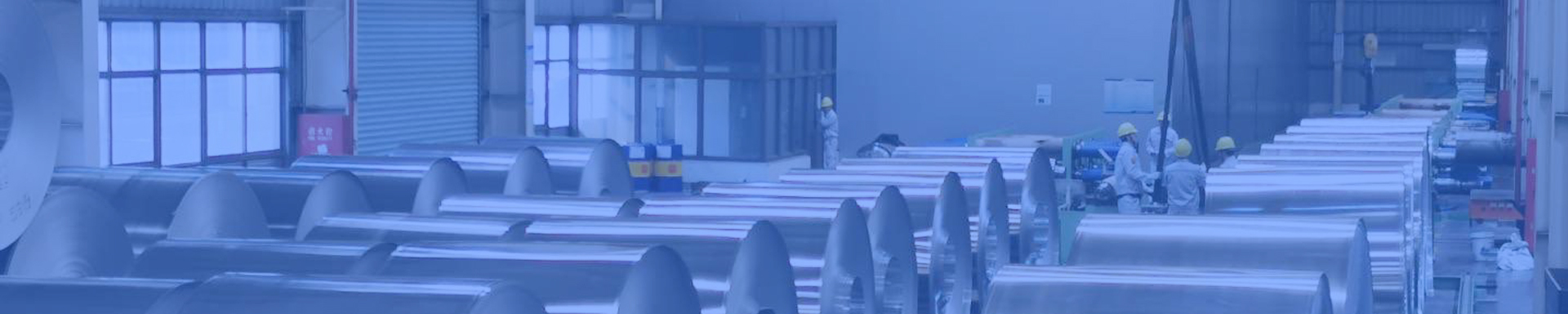
Non-ferrous Rolling Mill Machine Of The Casting Steel Bearing Support
Main products: All kinds of mill (roll) bearing block, bending roll block and other mill precision parts, the accuracy of these products directly affects the accuracy of the mill directly affects the quality of products produced by the mill.
The type is the bearing seat of mill work roll intermediate roll support roll, and can also accept other non-standard customizing from customers.
Material:
working roll (forgings):45 steel,40Cr,42CrMo
support roll (castings): zg310-570, zg270-500.
- Guangwei Manufacturing Precision
- China,Luoyang
- Contractual Stipulation
- Information
Non-ferrous Rolling Mill Machine Of The Casting Steel Bearing Support
Material selection of cast steel bearing seat for non-ferrous rolling mill
1. Common materials
Low alloy high-temperature cast steel (preferred choice):
ZG20CrMoV:
Ingredients: C 0.17-0.25%,Cr 1.0-1.5%,Mo 0.3-0.6%,V 0.1-0.3%;
Performance: High temperature strength (σ b ≥ 450MPa at 500 ℃), resistance to sulfide corrosion (annual corrosion rate<0.1mm in H ₂ S environment).
ZG1Cr18Ni9Ti (austenitic stainless steel): Used for strong corrosion conditions (such as seawater cooled rolling mills), but with high cost.
2. Material modification
Surface treatment:
Thermal spraying Al2O3-TiO2 coating (plasma spraying, thickness 0.3mm): corrosion resistance increased by 8 times;
Laser cladding of Ni60WC: The friction surface hardness reaches HRC60, and the service life is extended by three times.
The production and manufacturing technology process of cast steel bearing seats for non-ferrous rolling mills
1. Casting process
Mold design:
3D printed resin sand mold (precision CT8 level), with 2% shrinkage allowance reserved (ZG20CrMoV linear expansion coefficient 12.5 × 10 ⁻⁶/℃).
Melting and pouring:
Intermediate frequency furnace+LF refining (1600 ℃), adding rare earth elements (0.03% Ce) to purify the molten steel;
Bottom pouring (pouring temperature 1550 ℃), with heating agent covering the riser to prevent shrinkage.
Heat treatment:
Normalizing+tempering: 920 ℃ × 4h air cooling+650 ℃ × 6h, to eliminate casting stress (residual stress ≤ 80MPa).
2. Mechanical processing
Rough machining:
Longmen milling reference surface (flatness 0.08mm/m), deep hole drilling cooling water channel (Φ 25 ± 0.3mm).
Precision machining:
Bearing hole machining:
Rough boring (IT8 grade) → nitriding (hardness HV850) → precision boring (IT6 grade, roundness ≤ 0.01mm);
Mirror polishing of the inner surface (Ra ≤ 0.8 μ m) reduces friction.
3. Strengthening and testing
Surface strengthening:
Ion nitriding: 520 ℃ for 30 hours, with a layer thickness of 0.4mm (surface hardness HV950);
Vibration time response (VSR): eliminates machining stress (amplitude 0.5mm, frequency 50Hz).
Non destructive testing:
Industrial CT scan: detect internal pores (defect ≤ Φ 1.5mm);
Fluorescent penetrant testing (ASTM E1417): crack detection sensitivity of 0.01mm.
4. Assembly and anti-corrosion
Sealing system:
Adopting fluororubber sealing ring (temperature resistant to 250 ℃) and labyrinth sealing structure;
Anti corrosion coating:
Spray epoxy modified silicone resin (acid and alkali resistant, thickness 150 μ m).
Technology and Process Equipment
Scientific and reasonable arrangement of technological processing improves the accuracy, rationality and stability of product processing, and guarantees the quality.
CNC Machining Programming
Programmers use the PC simulation processing to run program, optimizating processing lines and reasonable arranging the processing tools, so that the processing of the workpiece more accurate with neat and beautiful knife lines.