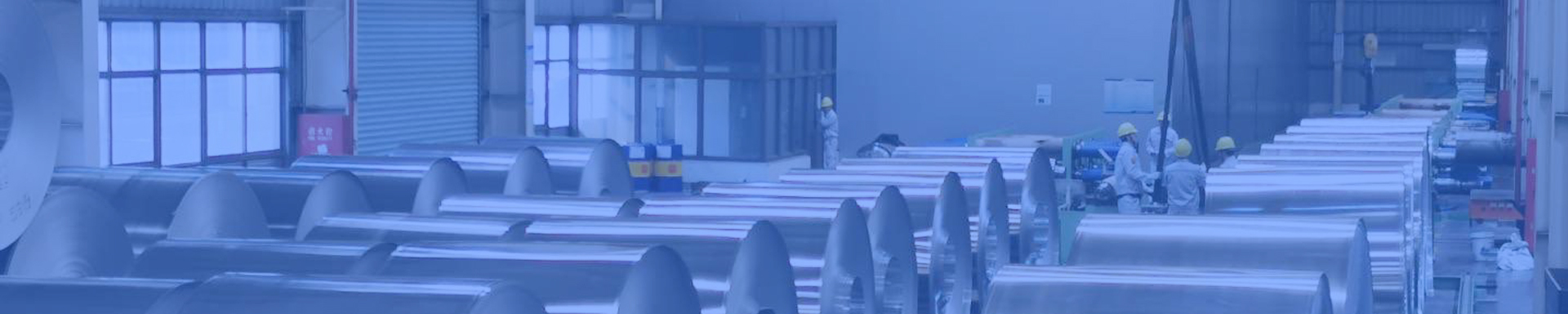
Customized 35CrMoV Steel Sleeve Of Cold Rolling Mill Machine
Mechanical properties of 35CrMoV steel sleeve(quenched and tempered: quenching+high-temperature tempering)
Typical value testing standards for performance indicators
Tensile strength (σ ₆) 900-1100 MPa GB/T 228.1 (ISO 6892)
Yield strength (σ ₀) ₂) 750–950 MPa
Elongation rate (δ) ≥ 12% with a gauge length of 5d (where d is the diameter of the specimen)
Impact energy (AKU) ≥ 50 J (at room temperature) GB/T 229 (ISO 148)
Hardness HRC 28-35 (quenched and tempered state) GB/T 230.1
Sectional shrinkage rate (ψ) ≥ 45%
- GW Precision
- China,Luoyang
- Contractual Stipulation
- Anual Capacity of Steel Spool is 4000 pieces
- Information
Customized 35CrMoV Steel Sleeve Of Cold Rolling Mill Machine
Steel Sleeve Material | Specification |
35CrMoV | Φ502*Φ560*1700 |
Comparison between 35CrMoV and other Cr Mo steels for Steel sleeve:
Brand carbon content (%) vanadium content (%) tensile strength (MPa) main advantages
35CrMoV 0.32-0.40 0.10-0.20 900-1100 comprehensive strength and toughness, low cost
42CrMo 0.38-0.45-1000-1200 has higher strength, but slightly lower toughness
34CrNiMo6 0.30-0.38-1000-1300 High toughness, fatigue resistance (including nickel)
Usage function of 35CrMoV steel sleeve (customized) for cold rolling mill
central role
Force transmission and support: The sleeve is used to connect the rolling mill and the transmission shaft, transmit rolling torque (up to 2000kN · m or more), and withstand radial rolling force (500-3000 tons).
Precise positioning: Ensure the coaxiality (≤ 0.02mm) between the rolling mill and the transmission system to avoid strip deviation or uneven thickness.
Anti fatigue and buffering: Relieve rolling vibration and impact loads (such as dynamic forces caused by sudden changes in flow rate).
Special needs
Wear resistance: The contact surface with bearings or rollers must withstand long-term sliding friction (surface hardness requirement HRC50-55).
Thermal stability: Maintain dimensional accuracy under cold rolling conditions (60-120 ℃) (thermal expansion coefficient needs to be matched with the rolling mill).
Production and manufacturing technology process of 35CrMoV steel sleeve (customized) for cold rolling mill
1. Forging process
Preparation of billets: ESR steel ingots are used to ensure low segregation (S, P ≤ 0.015%).
Forging Forming:
Multi directional forging (temperature 1100-850 ℃), forging ratio ≥ 4, eliminating casting defects;
Immediately normalize (880 ℃× 2h) after molding to refine the grain size.
2、Mechanical processing
Rough machining:
Lathe machining of outer circle and end face (with a margin of 2-3mm), drilling and tapping (thread accuracy of 6H level).
Semi precision machining:
Internal cooling channel for deep hole drilling (hole diameter Φ 15 ± 0.2mm, straightness ≤ 0.1mm/m);
Boring inner hole (IT7 precision, cylindricity ≤ 0.01mm).
3. Heat treatment strengthening
Quenching and tempering treatment:
Quenching (850 ℃ oil cooling)+high temperature tempering (550 ℃ × 4h), hardness HRC28-32 (core toughness guarantee).
Surface strengthening:
Ion nitriding: surface hardness ≥ HV900, infiltration layer 0.3-0.5mm (wear resistance increased by 5 times);
Alternatively, laser quenching can be used to selectively harden the contact surface (hardness HRC55-60, deformation<0.03mm).
4. Precision machining and testing
Grinding processing:
CNC cylindrical grinder precision grinding (dimensional tolerance ± 0.005mm, Ra ≤ 0.4 μ m);
Honing inner hole (roundness ≤ 0.005mm).
Testing items:
Ultrasonic testing (EN 10228-3 standard, no defects larger than Φ 1mm);
Residual stress detection (X-ray diffraction method, compressive stress layer ≥ 0.2mm).
We used our independent dedicated device-hole drilling machine which is researched and developed by ourselves, it also obtain the national patent.
The machine is provided with good rigid, no returning clamp and machine and high accuracy on the processing of machining. Through continuous improvement, our company formed a integrated processing technic system to ensure concentricity, cylindricity, degree of symmetry and dynamic balance of the steel sleeve. Specific accuracy tolerance and geometric accuracy tolerance is strictly according to the customers’ requires.