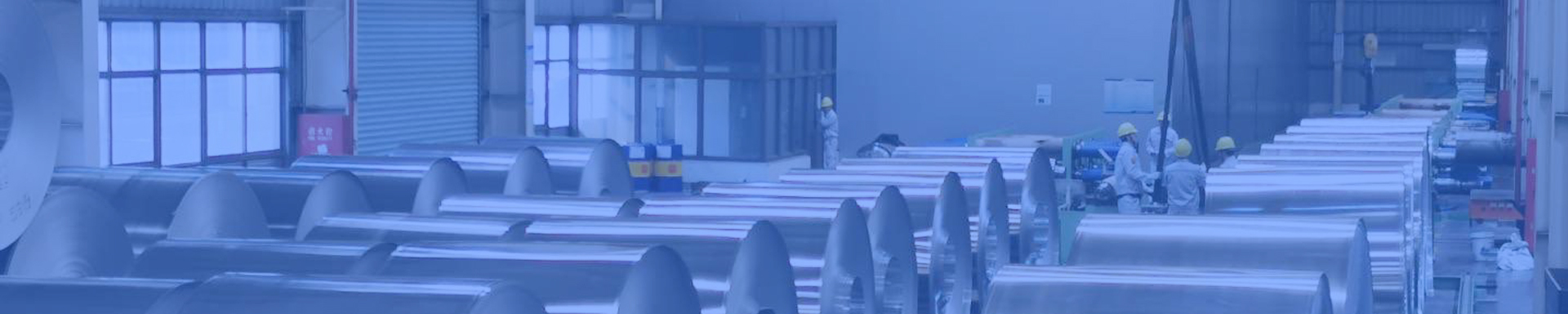
Cold Rolling Mill Machine Of The Drive side work roll mill bearing seat
Material Science:
Cold Rolling Mill Machine Of The Drive side work roll mill bearing seat(forging): 40Cr,
They are a guarantee of high-quality cold rolling mill machine of the drive side work roll mill bearing seat products.
The bearing installation hole is the core part and requires high dimensional accuracy. The diameter of the installation hole should be accurately matched with the outer diameter of the bearing to ensure tight installation and no looseness or deviation during operation. Its surface roughness also has strict requirements, and a smooth surface can reduce installation friction and facilitate heat dissipation.
- Guangwei Manufacturing Precision
- China,Luoyang
- Contractual Stipulation
- Information
Cold Rolling Mill Machine Of The Drive Side Work Roller Rolling Mill Block Shaft
Application scenarios of the bearing seat for the working roll mill on the drive side of the cold rolling mill
(Suitable for high-precision plate and strip cold rolling mill)
1. Core functions
Dynamic load support: withstand rolling force (800-2500kN) and bending roll force (± 500kN), ensuring roll gap accuracy of ± 0.005mm
Torque transmission: Transmit the driving torque of the motor (peak value can reach 150% of the rated value), suitable for rolling speeds of 10-40m/s
Vibration control: Suppress high-frequency vibrations during high-speed rolling (vibration acceleration ≤ 4.5m/s ², ISO 10816-3)
2. Extreme working conditions
Mechanical stress:
Cyclic contact stress 900-1300MPa (Hertz contact theory)
Roll change impact load (instantaneous acceleration 10-15g)
Environmental challenges:
Rolling oil penetration (sulfur-containing extreme pressure additive)
Aluminum/stainless steel debris abrasive wear (hardness HV400-1200)
Material selection and strengthening of the bearing seat for the working roll mill on the drive side of the cold rolling mill
1. Base material
Material grade, core advantages, applicable scenarios
ZG35CrMnSi high fatigue strength (σ -1 ≥ 380MPa) ordinary carbon steel cold-rolled
ZG25CrNiMo impact resistance (Akv ≥) 60J@-20 High strength steel rolling (℃)
ZG06Cr13Ni4Mo corrosion-resistant (C ≤ 0.06%) stainless steel/aluminum rolling
2. Strengthening of key areas
Bearing installation holes:
Ion nitriding (layer depth 0.3-0.5mm, hardness HV900-1100)
Precision honing (roundness ≤ 0.005mm, Ra ≤ 0.1 μ m)
Sealing surface:
Laser cladding of Ni based alloy (Inconel 625, resistant to micro motion wear)
3. Heat treatment system
Quenching and tempering treatment:
Quenching: 880 ℃ × 2h (polymer quenching solution)
Tempering: 550 ℃ × 4h (two rounds of tempering)
Dimensional stabilization:
Cryogenic treatment (-80 ℃ × 12h)
Time treatment (180 ℃ × 24h)
4. Surface engineering
Composite coating:
Sandblasting (Sa3.0 grade)
Arc spraying Cr3C2 NiCr (thickness 150-200 μ m)
Laser remelting (porosity<0.3%)
The primary function of a cold rolling mill machine of the drive side work roll mill bearing seat is to ensure precise alignment of the bearing during operation and to withstand the applied radial and axial loads. Additionally, it reduces the clearance between the bearing and shaft while minimizing frictional losses.
Quality process control
The cold rolling mill machine of the drive side work roll mill bearing seat we manufacture are inspected by inspectors at every step from rough processing, flaw detection, heat treatment to production process. Only after passing the inspection can we proceed to the next processing step.