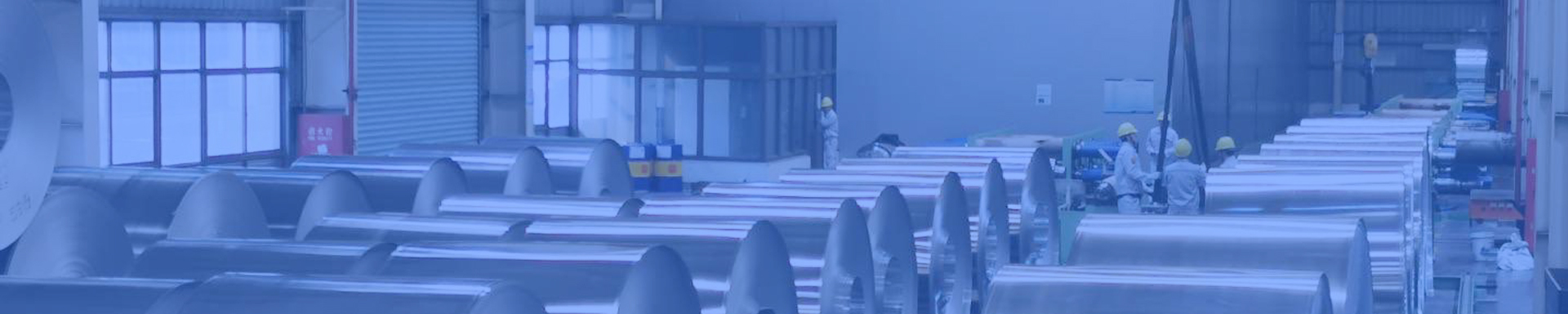
Cold Rolling Mill Machine Of The Operate Side Work Roller Bearing Block
Core functions and working condition requirements of the working roll bearing seat on the operating side of the cold rolling mill
Core functions
High precision positioning: Ensure that the radial runout of the work roll is ≤ 0.01mm (with a thickness tolerance of ± 1 μ m for thin strip steel rolling)
Quick roll change: Integrated hydraulic locking mechanism (roll change time ≤ 10 minutes)
Vibration suppression: Control high-frequency vibrations at 20-500Hz (amplitude ≤ 0.5 μ m)
Compatible models
Six roll UC-MILL: Rolling thickness of 0.1-2.0mm stainless steel/silicon steel
Twenty roll Sendzimir rolling mill: production of ultra-thin strip (0.02-0.2mm)
- GW Precision
- China,Luoyang
- Contractual Stipulation
- Anual Capacity is 1000 pieces
- Information
Cold Rolling Mill Machine Of The Operate Side Work Roller Bearing Block
Material and Heat Treatment Specification for the working roller bearing seat
Main material
Brand: QT600-3 ductile iron (EN-GJS-600-3)
Ingredient optimization:
|Element | C 3.6-3.8 | Si 2.2-2.5 | Mn ≤ 0.3 | Mg 0.03-0.05|
Performance characteristics:
Damping characteristics (vibration attenuation rate ≥ 35%)
Better strength/weight ratio than cast steel (density 7.1g/cm ³)
Working roller bearing seat key component materials
Component material heat treatment surface treatment
Working roller bearing seat body QT600-3 isothermal quenching shot peening strengthening (0.3mA)
Wear resistant lining GCr15SiMn deep cold treatment with hard chromium plating (20 μ m)
Sealing component PTFE+316L - laser microtexture
GW precision working roller bearing seat heat treatment process
Isothermal quenching:
900 ℃× 2h → Salt bath quenching (300 ℃× 1h) → Air cooling
Dimensional stability treatment:
180 ℃ × 24h aging (size change ≤ 0.005%)
1、 Vertical Machining Center: According to the view shape milling depth 5mm to find the positive belt (each side has room for 1.5-2mm); clean and remove burr sharp edge for inspection. (first piece for inspection)
2、 Horizontal boring machine :It is found that a margin of 1.5 -2 mm is reserved for each surface of the normal belt, and the margin of the groove in the view is 1.5-2 mm; the margin of the hole in the hole is 3-4 mm; the length of each hole is 2-3mm; and the clear edge is used for removing the sharp edge of the burr for inspection. (first piece for inspection)
3、 Vertical Machining Center: Finish milling to (non-tolerance fit surface) requirements, milling length to find the right edge depth of 5 mm; boring to the requirements, each side of the residual amount of 1 ≤ 1.5 mm; each hole length to the requirements, and point to the two ends of the hole center hole; to ensure the dimensional tolerance and shape and position tolerance.
4、 Horizontal machining center: upper tooling, alignment length and alignment edge are based on the middle hole, and all sides meet the requirements;And point the center hole of each hole on the end face to ensure the tolerance of each dimension and form;Hole deep processing to requirements;Ensure dimensional tolerance;
5、 Vertical Machining Center: To the original hole as a benchmark, fine boring hole, to the requirements;Hole processing according to the difference, and then use a rolling knife rolling hole surface;To ensure the tolerance of each hole, a test shall be conducted to keep the allowance of 1mm before machining to the dimension.Clean and remove sharp edges of burrs for inspection.
6、 Bench-work:Each thread bottom hole positioning hole to requirements.
7、 Bench-work: Other oil hole and screw hole drilling tapping;Clean and remove sharp edges of burrs for inspection. (first piece for inspection)
8、 Final inspection: remove sharp edges of burrs by cleaning and send for inspection, and issue inspection list.
Mechanical machining accuracy of working roller bearing seat
Critical dimensional tolerances
Testing method for tolerance level of machining parts
Bearing hole (Φ 200-400mm) IT4 electronic plug gauge+roundness tester
Hydraulic cylinder installation surface flatness 0.01mm optical flat crystal
Positioning pin hole H6 level coordinate measuring machine
Positional tolerance
Bearing hole cylindricity ≤ 0.003mm
Verticality of each installation surface ≤ 0.005mm/100mm
Perfect quality management system, effective after-sales service guarantee, so that the company's working roller bearing seat products won a good reputation.
Lubrication and sealing system for the working roler bearing seat
Oil air lubrication system
Oil: ISO VG 68 synthetic ester (containing MoS ₂ additive)
Parameters:
Oil volume 0.05ml/time
Air pressure 0.4-0.6MPa
Frequency 2-5Hz (automatically adjusted with rolling speed)
Multi stage sealing
First step: Magnetic fluid seal (pressure resistance of 0.15MPa)
Second step: Silicon carbide mechanical seal
Third step: Maze style gas seal (N2 protection)