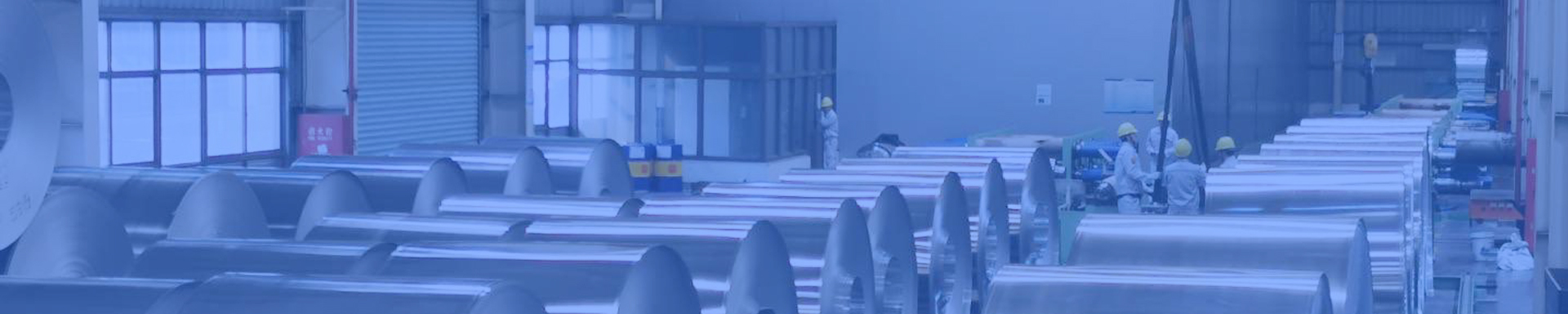
Intermediate Roller Bearing Chock Of Hot Mill Machine
GW precision Advantages:
high-precision intelligent CNC manufacturing equipment, high-tech staff, mature processing system, strict quality inspection process, excellent production management process, is the guarantee of high-quality products.
In order to better ensure the quality of products, in addition to the regular size inspection, the company bought a high-precision mobile bridge type three-position standard measuring machine, the detection accuracy up to 2 micron level, to ensure the absolute inspection basis of various parts size and behavior tolerance inspection.
- Guangwei Precision
- China,Luoyang
- Contractual Stipulation
- Anual Capacity of Steel Spool is 4000 pieces
- Information
Intermediate Roller Bearing Chock Of Hot Mill Machine
The bearing seat of the intermediate roll in the hot rolling mill is a key component in the hot rolling production line, mainly used to support and fix the intermediate roll, withstand huge rolling force, impact force, and high temperature environment.
Application scenarios of intermediate roller bearing seat in hot rolling mill
work environment
High temperature: During the hot rolling process, the temperature of the rolling mill can reach over 800 ℃, and the bearing seat needs to withstand radiation heat and conduction heat.
High load: capable of withstanding rolling forces (up to thousands of tons) and frequent impact loads.
Dusty/humid: Rolling cooling water and iron oxide scale are prone to invasion, requiring high sealing and corrosion resistance.
Functional requirements
Accurate positioning: Ensure the parallelism and rolling accuracy of the rolling mill rolls.
Wear resistant and fatigue resistant: prolongs service life and reduces downtime maintenance.
Lubrication guarantee: A high-pressure lubrication system (such as oil air lubrication) is required to reduce friction and wear.
Heat treatment process of intermediate roller bearing seat in hot rolling mill
Heat treatment is a key step in improving the mechanical performance of bearing seats, usually including the following steps:
Pre treatment (normalizing or annealing)
Eliminate internal stress in forgings or castings, refine grain size, and prepare for subsequent processing.
Quenching+tempering (quenching and tempering treatment)
Quenching: Heating to a critical temperature (such as 850-900 ℃) and then rapidly cooling (water quenching or oil quenching) to obtain a high hardness martensitic structure.
Tempering: Medium temperature tempering (400-600 ℃) is used to balance hardness and toughness, avoiding brittle fracture.
Surface strengthening (optional)
Induction hardening: Local hardening of the bearing contact surface to improve wear resistance.
Carburizing/nitriding: suitable for high alloy steel, enhancing surface hardness and fatigue resistance.
Stress relief annealing
After precision machining, low-temperature annealing (200-300 ℃) is carried out to eliminate machining stress.
GW Precision manufacture all kinds of Intermediate Roll Bearing Chock and other mill precision parts.
GW precision Advantages:
high-precision intelligent CNC manufacturing equipment, high-tech staff, mature processing system, strict quality inspection process, excellent production management process, is the guarantee of high-quality products.