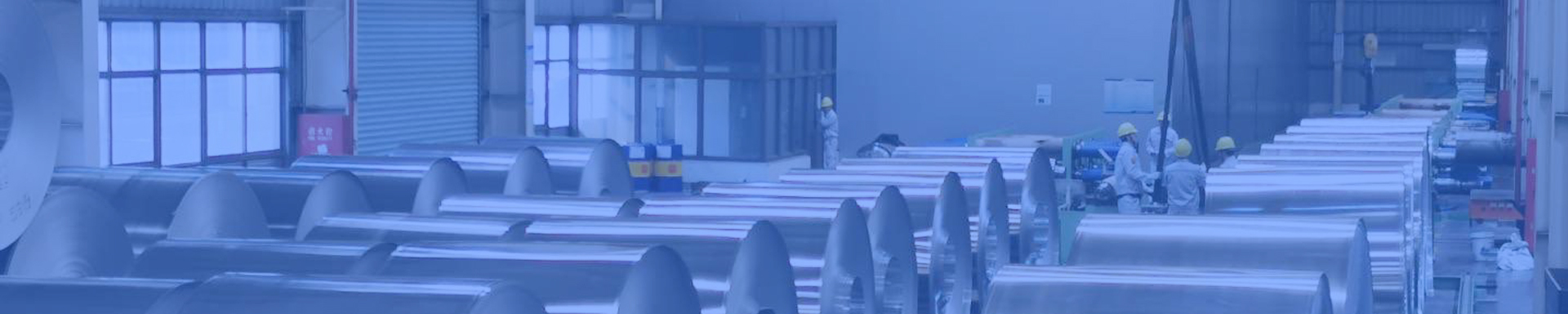
Hot Rolling Mill Machine Of The Drive Side Intermediate Roller Bearing Block
The core function of the intermediate roller bearing seat on the drive side of the hot rolling mill
Support and positioning: Accurately fix the middle roller, bear the rolling force and transmit it to the frame.
Power transmission: Connect the universal shaft or gearbox on the driving side to transmit the motor torque to the rolling mill.
Lubrication and sealing: Integrated oil air lubrication system to prevent cooling water and oxide scale from entering the bearings.
- GW Precision
- China,Luoyang
- Contractual Stipulation
- Anual Capacity is 1000 pieces
- Information
Hot Rolling Mill Machine Of The Drive Side Intermediate Roller Bearing Block
The intermediate roller bearing seat on the drive side of the hot rolling mill is one of the core components of the rolling mill, mainly used to support and position the intermediate roller, withstand high loads, impacts, and heat conduction during the rolling process.
Application scenarios of drive side intermediate roller bearing seat for hot rolling mill
work environment
High temperature (rolling zone can reach 800-1200 ℃), high humidity (cooling water/lubricant), high dust
Capable of withstanding rolling forces (up to thousands of tons), alternating loads, and vibrations
Long term continuous operation is required, with a short maintenance cycle (usually synchronized with roll replacement)
Functional requirements
Accurately maintain bearing clearance to prevent roll deflection
Effectively conduct bearing heat (avoid overheating failure)
Resistance to wear and micro motion wear (bearing and seat hole mating surface)
Compatible with hydraulic bending roller system (some models require additional axial force)
Performance characteristics of the intermediate roller bearing seat on the drive side of the hot rolling mill
texture of the intermediate roller bearing seat material:
Cast steel (ZG35CrMo or ZG42CrMo): Balancing strength and casting processability.
Forged steel (34CrNiMo6): used for ultra-high load models, with better fatigue resistance.
Internal cooling channel: circulating water or air cooling to reduce bearing temperature rise.
The company has formed a set of mature mechanical processing technology for the production of the intermediate roller bearing seat through the accumulation of long-term experience:
1、 Vertical Machining Center: According to the view shape milling depth 5mm to find the positive belt (each side has room for 1.5-2mm); clean and remove burr sharp edge for inspection. (first piece for inspection)
2、 Horizontal boring machine :It is found that a margin of 1.5 -2 mm is reserved for each surface of the normal belt, and the margin of the groove in the view is 1.5-2 mm; the margin of the hole in the hole is 3-4 mm; the length of each hole is 2-3mm; and the clear edge is used for removing the sharp edge of the burr for inspection. (first piece for inspection)
In the production process of rolling mill bearing seat bending roll block and other products, the optimized processing program is compiled by computer, and the process plan is arranged reasonably, which ensures the The drive side intermediate roller bearing block product quality to reach the international first-class standard.