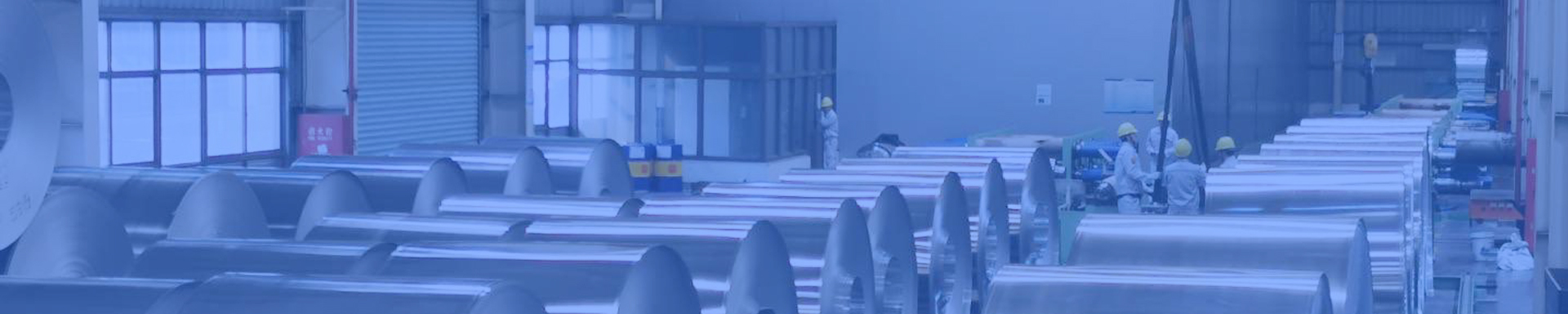
Rolling Mill Bearing Block Of Working Roller Of Hot Mill Machine
GW Precision has formed a set of mature mechanical processing technology for the production of bearing housing through the accumulation of long-term experience.
GW Precision rolling mill bearing block often use the following materials:
1. Cast steel: durable and high price. Rolling mill bearing housings are mainly made of cast steel.
2. Gray cast iron: economical and cheap, but not durable .
3. Ductile cast iron: has a certain degree of strength, plasticity and toughness .
4. Stainless steel: This material is being used on the work conditions where there is corrosion .
5.Zinc alloy: lightweight, easy to install, corrosion-resistant, maintenance-free, and has vibration and
shock absorbing properties.
Choosing the right material will ensure that the mill bearing housing can still maintain good performance
and long service life under harsh working conditions.
- GW Precision
- China,Luoyang
- Contractual Stipulation
- Anual Capacity of Steel Spool is 4000 pieces
- Information
Rolling Mill Bearing Block Of Working Roller Of Hot Mill Machine
GW Precision has formed a set of mature mechanical processing technology for the production of
bearing housing through the accumulation of long-term experience.
GW Precision rolling mill bearing block often use the following materials:
1. Cast steel: durable and high price. Rolling mill bearing housings are mainly made of cast steel.
2. Gray cast iron: economical and cheap, but not durable .
3. Ductile cast iron: has a certain degree of strength, plasticity and toughness .
4. Stainless steel: This material is being used on the work conditions where there is corrosion .
5.Zinc alloy: lightweight, easy to install, corrosion-resistant, maintenance-free, and has vibration and
shock absorbing properties.
Choosing the right material will ensure that the mill bearing housing can still maintain good performance
and long service life under harsh working conditions.