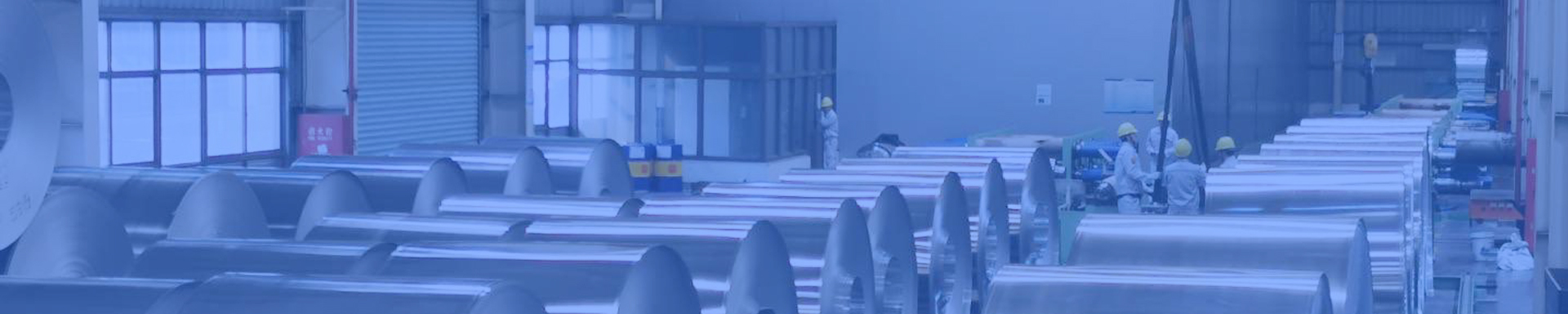
roller
GW Precision rolling mill roller is an important part in the rolling mill, the use of a pair or a group of GW Precision rolling mill rollers rolling pressure to roll mill steel. GW precision rolling mill roller are mainly subjected to rolling dynamic and static loads, wear and temperature changes.
- GW Precision
- China,Luoyang
- Contractual Stipulation
- Anual Capacity is 500 pieces
- Information
The selection and manufacturing of rolling mills roller require comprehensive consideration of the type of rolling mill, rolling materials, and operating conditions. High chromium cast iron and high-speed steel rollers are suitable for high wear resistance scenarios, while forged steel rollers are more suitable for high load rough rolling. Strict control of heat treatment and machining accuracy is required in manufacturing to ensure thermal fatigue resistance and wear resistance.
Hot rolling mill rollers are the core components in hot rolling production lines, mainly used to roll metal billets into desired shapes and sizes of plates, strips, or profiles under high temperature conditions.
GW Precision rolling mill roller is an important part in the rolling mill, the use of a pair or a group of GW Precision rolling mill roller pressure to roll mill steel. It is mainly subjected to rolling dynamic and static loads, wear and temperature changes.
Commonly used work roller material of cold rolls are 9Cr, 9Cr2, 9Crv, 8CrMoV, etc.. Cold rolling requires surface quenching and hardness of HS45~105.
Hot rolls commonly used materials 55Mn2.55Cr.60CrMnMo.60SiMnMo, etc.. The hot rolls used in the opening of the bad thick plate, section steel and other processing. It is subjected to a strong rolling force, intense loss and thermal fatigue effects, and hot rolls work at high temperatures, and allows the unit workload within the diameter of the wear and tear, so do not require the surface hardness, only requires a high strength, toughness and heat resistance. Hot rolls only use the whole normalized or quenched, surface hardness requirements HB190 ~ 270.
Key parameters for the production and manufacturing of hot rolling rolls
Chemical composition (taking high chromium cast iron as an example):
C: 2.5~3.5%, Cr: 12~20%, Mo: 1~3%, Ni: 0.5~1.5%, V: 0.5~1.5%。
Heat treatment process:
Quenching: Oil quenching or air cooling at 950~1050 ℃ to increase hardness.
Tempering: 400~550 ℃ to relieve stress and balance toughness and hardness.
Cryogenic treatment (optional): -70~-196 ℃ to enhance residual austenite transformation.
Mechanical properties:
Hardness: The surface hardness of the finishing roll is ≥ 70 HS (Shore hardness), and the surface hardness of the roughing roll is ≥ 55 HS.
Tensile strength: ≥ 800 MPa (forged steel rollers can reach over 1200 MPa).
Impact toughness: ≥ 15 J/cm ² (core requirement).
Manufacturing process:
Casting: Centrifugal casting is used for composite rollers (outer wear-resistant material+core tough material).
Forging: Steel rollers require multi-directional forging to refine grain size.
Processing accuracy: roller diameter tolerance ± 0.05mm, roughness Ra ≤ 0.8 μ m.
Cooling and lubrication:
Internal water cooling of the rolling mill (water temperature 20-40 ℃, flow rate ≥ 5m/s).
Rolling lubrication uses graphite or synthetic lubricants to reduce steel sticking.