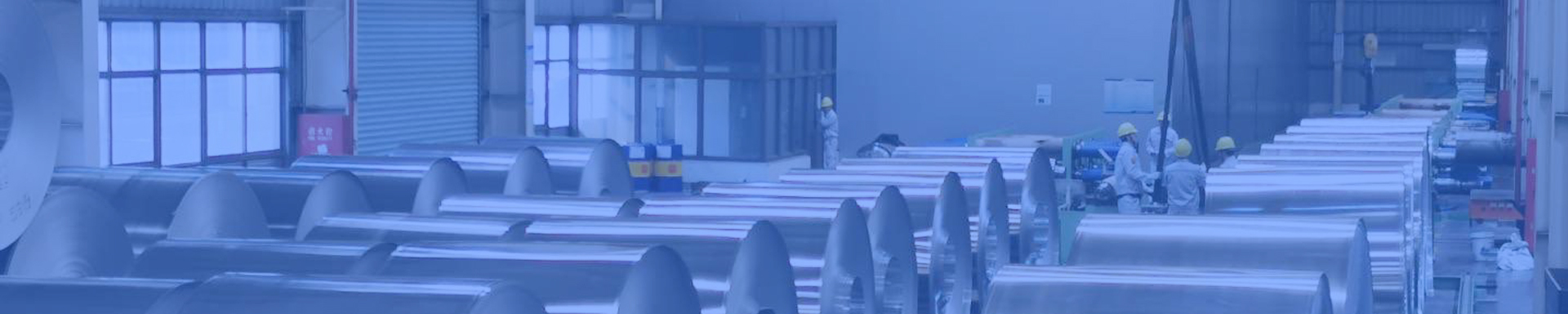
Cold Rolling Mill Machine Of The Transimit Side Supporting Roller Bearing Support
Mostly made of cast steel or 45 # steel material, meeting high load-bearing requirements through non-standard customization
In order to better ensure the quality of products, in addition to the normal size inspection, bearing and other precision parts in the three coordinate standard measuring machine instrument for final inspection,
- Guangwei Manufacturing Precision
- China,Luoyang
- Contractual Stipulation
- Information
Cold Rolling Mill Machine Of The Transimit Side Supporting Roller Bearing Support
Luoyang Guangwei precision technology co.ltd,. locates on the west side of the Henan Diesel plant, one of ten greatest plant during the First Five-year Plan in Henan province. Spools are our main products.
Bearing installation hole
This is the core part, which requires high dimensional accuracy. The diameter of the installation hole should be accurately matched with the outer diameter of the bearing to ensure tight installation and no looseness or deviation during operation. Its surface roughness also has strict requirements, and a smooth surface can reduce installation friction and facilitate heat dissipation.
The bearing pedestal of the transfer side support roll of the cold rolling mill is the core bearing part of the rolling mill, which is directly related to the rolling accuracy and equipment stability.
Application Scenarios of Transfer Side Support Roll Bearing Pedestal of Cold Rolling Mill
Core functions
The support rolls are precisely supported on the transfer side (operating side/drive side) of the cold mill to withstand rolling forces up to 2000-5000 tonnes.
Ensure the rigidity of roller system and control panel with thickness tolerance (± 0.005mm level).
Operating condition characteristics
Load type: high-frequency alternating load (rolling force fluctuation)+impact load (strip steel bite/uncoupling).
Environmental challenges: Emulsion splash (pH 5-9), ingress of metal dust, corrosion protection and seal protection.
Precision requirements: coaxiality of bearing hole ≤ Φ 0.02mm, flatness of bottom ≤ 0.03mm/m.
Material selection of support roll bearing seat on conveying side of cold rolling mill
Main material
High-strength cast iron (economical scheme):
Brand: QT600-3 (nodular cast iron), tensile strength ≥ 600MPa, hardness HB220-280.
Advantage: good shock absorption, suitable for small and medium-sized rolling mill.
Alloy cast steel (preferred for heavy duty):
Brand: ZG35Cr1Mo (0.8-1.2% Cr added), yield strength ≥ 450MPa, good weldability.
Forged Steel (Ultra High Strength Requirement):
Brand: 34CrNiMo6 (VOD refining), used for high-speed rolling mill (linear speed>20m/s).
Wear-resistant parts
Bearing Liner Plates:
Material: CuZn25Al5 (copper alloy) or PTFE composite material (self-lubricating).
Sealing groove:
Surface overlaying Stellite 6 alloy (HRC ≥ 55), abrasion resistant.
Heat Treatment Process of Support Roller Bearing Pedestal on Transfer Side of Cold Rolling Mill
Iron casting parts
Isothermal annealing: 920 ℃ × 4h → furnace cooling to 740 ℃ × 6h, eliminating casting stress (residual stress ≤ 50MPa).
Surface quenching: the bearing hole is subject to intermediate frequency quenching (HRC48-52, layer depth of 2-3mm).
Cast Steel/Forged Steel Parts
Conditioning and tempering treatment:
Quenching: 850 ℃ oil cooling (forged steel shall be pre-cooled to 800 ℃ for crack prevention).
Tempering: 620 ℃ × 4h, hardness: HB280-320.
Local nitriding: gas nitriding of sealing faces (HV800, 0.2mm deep).
Through the above process, the bearing seat of the cold rolling mill can achieve a service life of 10-15 years, support the rolling capacity of over one million tons, and reduce the comprehensive cost by 20% - 30%.