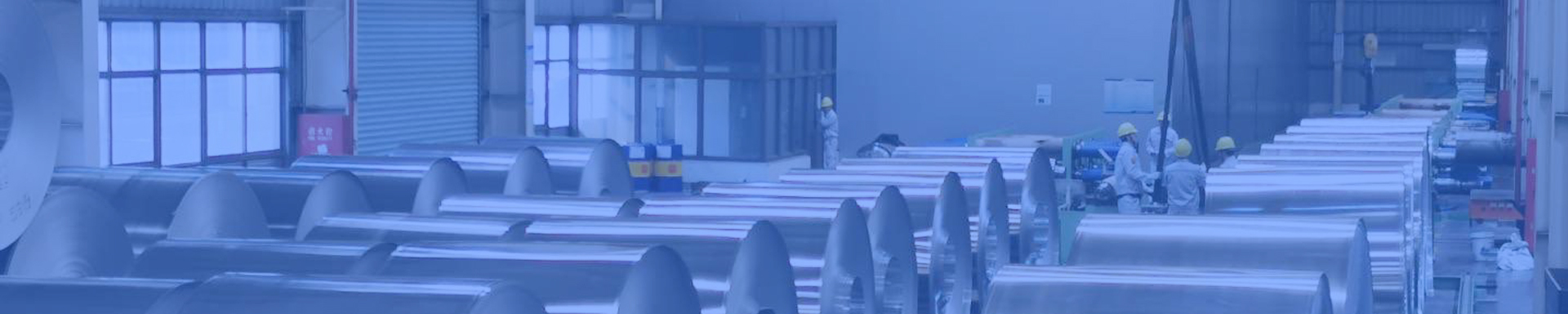
Customized Centrifugal Casting Steel Spool Of Copper Sheet And Strip Mill Machine
Which material will be used for centrifugal casting steel?
One suggested material is 35CrNiMo, and the specification is 685*605*700.
- GW Precision
- China,Luoyang
- Contractual Stipulation
- Anual Capacity of Steel Spool is 4000 pieces
- Information
Customized Centrifugal Casting Steel Spool Of Copper Sheet And Strip Mill Machine
Which material will be used for casting steel?One suggested material is 35CrNiMo, and the specification is 685*605*700.
35CrNiMo is a high-strength alloy steel with excellent comprehensive mechanical properties (high strength, high toughness, good hardenability, and fatigue resistance). The sleeve produced by centrifugal casting process can further improve the density of the structure and the uniformity of mechanical properties.
Application scenario of customized 35CrNiMo centrifugal cast steel sleeve for copper strip rolling mill
In copper strip rolling mills, 35CrNiMo centrifugal cast steel sleeves are mainly used for the following key parts:
Roller bearing seat: supporting the roller and bearing the rolling force, it needs to resist the high pressure and alternating load during copper strip rolling.
Transmission connecting components: transmitting torque, requiring high torsional strength and wear resistance.
High temperature and high stress environment: During hot rolling of copper strip, the sleeve needs to maintain stability at 300-500 ℃ (depending on heat treatment and alloy design).
Advantages:
Centrifugal casting eliminates pores and slag inclusions, resulting in a denser structure;
The Ni Cr Mo synergistic effect of 35CrNiMo enhances low-temperature toughness and impact resistance.
Heat treatment process for customized 35CrNiMo centrifugal cast steel sleeve for copper strip rolling mill
1. Preliminary heat treatment (casting state adjustment)
Diffusion annealing: Hold at 1050-1100 ℃ for 10-12 hours to eliminate dendrite segregation, cool in the furnace to 600 ℃ and then air cool.
Normalization: Air cooling at 880-900 ℃ to refine grain size and prepare for subsequent quenching.
2. Final heat treatment (quenching and tempering)
Quenching: Oil quenching at 850~870 ℃ (water quenching+oil cooling dual medium quenching required for thickness>100mm), ensuring full section quenching.
Tempering: Temper at 560~600 ℃ for 3~4 hours to obtain tempered martensite, with hardness controlled at HRC 28~32.
3. Surface strengthening (optional)
Induction hardening: High frequency quenching of the contact surface to HRC 50-55, with a depth of 2-3mm.
Carburizing: Perform deep carburizing (1.0-1.5mm) on parts that require extremely high wear resistance.
GW Precision adopts advanced smelting and casting technology, with the equipment accurately inspected to ensure the chemical composition of the centrifugal casting steel material is reliable and accurate,meanwhile has the same characteristics.
Centrifugal casting will guarantee the inner and outer surface of the casting steel sleeve is free from defects such as cracks, slag inclusion, pores and sand holes.
Heat treatment of GW precision customized steel sleeve:
We will conduct heat treatment strictly for steel sleeve which have the specific demand in mechanical property, also in corresponding testing of the mechanical property, make sure every product to achieve the best condition and customers’ good results.