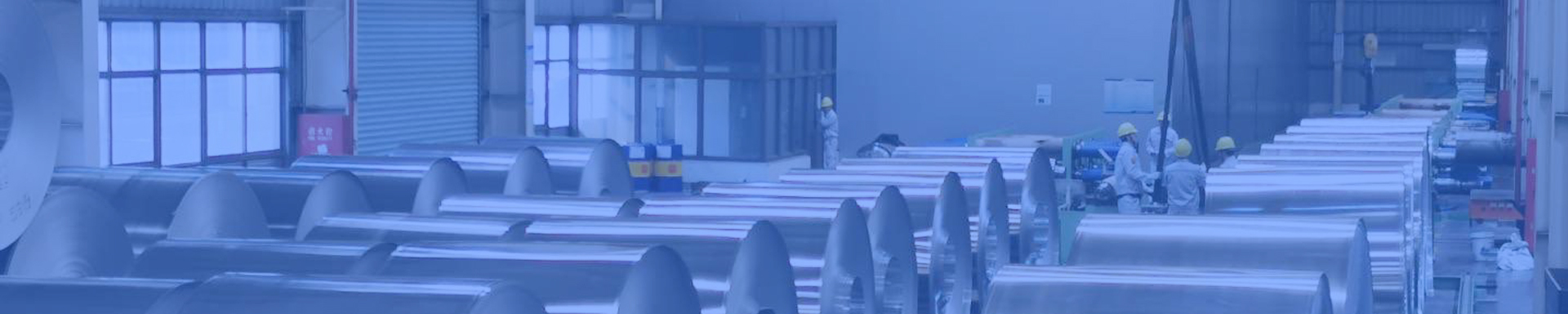
Cast steel working side bearing seat
GW precision Cast steel working side bearing seat Material:
working roll (forgings):45 steel,40Cr,42CrMo
support roll (castings): zg310-570, zg270-500.
- Guangwei Manufacturing Precision
- China,Luoyang
- Contractual Stipulation
- Information
Ferrous Rolling Mill Machine Of The Casting Steel Bearing Block
Application scenarios of cast steel working side bearing seat
(Suitable for hot/cold rolling mill roll support)
1. Core functions
Roll positioning: Accurately maintain the radial/axial position of the work roll (positioning accuracy ± 0.1mm)
Load transmission: withstand rolling force (maximum 25MN) and impact load (such as instantaneous impact coefficient of 2.5 for biting steel)
Thermal management: Stable operation at 200-600 ℃ (resistant to thermal deformation)
2. Typical working conditions
Mechanical stress:
Cyclic contact stress 800-1200MPa (Hertz theoretical calculation value)
Vibration acceleration>5m/s ² (ISO 10816-8 standard)
Environmental challenges:
Iron oxide scale abrasive wear (hardness HV800-1100)
Corrosion of rolling cooling water (pH 6-9, Cl ⁻ ≤ 50ppm)
Material selection and optimization of cast steel working side bearing seat
1. Base material
Material grade characteristics advantages Applicable scenarios
ZG270-500 low cost, good shock absorption, small and medium-sized cold rolling mill
ZG35CrMo high-strength (σ b ≥ 750MPa) hot rolling roughing mill
ZG06Cr13Ni4Mo corrosion-resistant (C ≤ 0.06%) stainless steel rolling line
2. Strengthening of key areas
Bearing installation holes:
Surface high-frequency quenching (hardness HRC50-55, layer depth 3-5mm)
Hard chrome plating (30-50 μ m)+precision grinding (Ra ≤ 0.2 μ m)
Sealing groove: Laser cladding Co based alloy (Stellite 6, resistant to micro motion wear)
3. Adaptation to special working conditions
Tropical rolling mill: adding Nb/V microalloying (improving high-temperature strength)
Coastal factory: using Cu-P-Cr weather resistant cast steel (salt spray corrosion resistant)
Heat treatment
Normalization+Tempering:
Normalization: 900 ℃ × 4h (air-cooled)
Tempering: 580 ℃ for 6 hours (eliminating over 90% of residual stress)
Local reinforcement:
Induction hardening of bearing holes (power density ≥ 5kW/cm ²)
Inspection and assembly
Qualified indicators for testing project method standards
Internal defects ASTM E186 radiographic testing level 2 or below
Dimensional accuracy CMM measurement hole spacing tolerance ± 0.02mm
Dynamic Balance ISO 1940-1 G6.3 Level
In order to better ensure the quality of products, in addition to the normal size inspection, bearing and other precision parts in the three coordinate standard measuring machine instrument for final inspection, detection accuracy up to 2 micron level, to ensure the absolute inspection of various parts size and behavior tolerance inspection basis.